Nomad Global Communication Solutions, Inc.
There are presently no open calls for resumes.
< Back
Nomad GCS is a dynamic team of problem solvers and change makers.
Join us.
Make a Difference
Customers in defense, public safety, energy, healthcare, education, and private sector business rely on Nomad to keep them connected and operational when every minute matters. Their missions protect commerce, property, and lives. Their challenges are complex.
A career at Nomad truly benefits the greater good. From engineering, fabrication, and IT, to operations, finance, and service… Every role is critical. Your teammates will trust and rely on you. Our customers will see and appreciate the attention to detail in your work. It will make their jobs easier, safer, and more effective every day.
This work matters.
//
Grow and Prosper
Our mindset is rooted in growth. We give customers solutions for today, on a platform that evolves with them into the future. In the same way, you’ll have opportunities at Nomad to expand your skillset and advance your knowledge. We’re guided not by a one-size-fits-all playbook, but by the understanding that a group of people driving with purpose toward individual goals makes a strong team.
What do you want to learn?
//
Work in Paradise
If you live here or have visited, you already know. Northwest Montana is a special place. We’re fortunate to have unspoiled wilderness, free-flowing rivers, and tight-knit communities as a backdrop for our work. So, in addition to competitive pay, opportunities for growth, compelling benefits like medical and dental insurance, a matching 401(k) retirement plan, and other perks… You’ll find four-season recreation, art, culture, and incomparable quality of life in the Flathead Valley.
Find yourself in Montana.
//
The fine print: Nomad Global Communication Solutions, Inc. strives to ensure equal opportunities for all applicants and employees. Human resources decisions are based upon job-related criteria, without regard to race, color, national origin, religion, gender, age, or any other protected status. Nomad promotes a safe, respectful, and drug-free work environment.
//
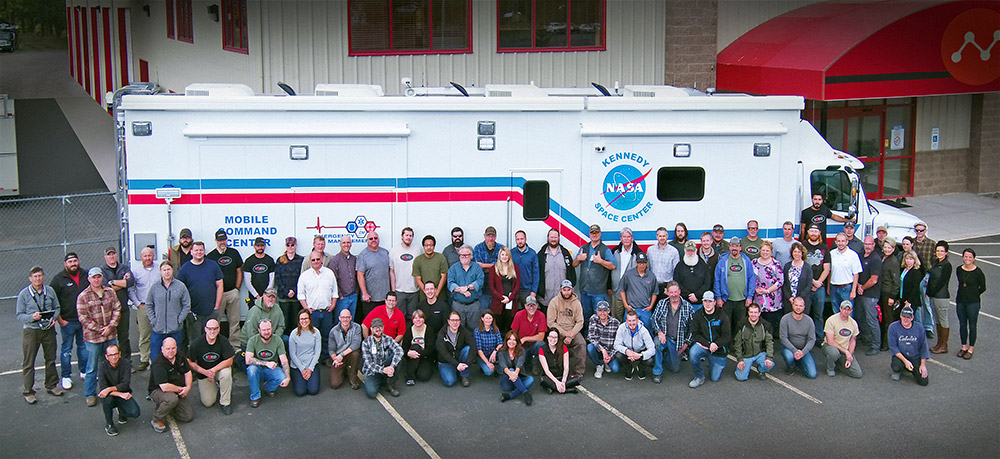